What Is Total Dynamic Head (TDH)?
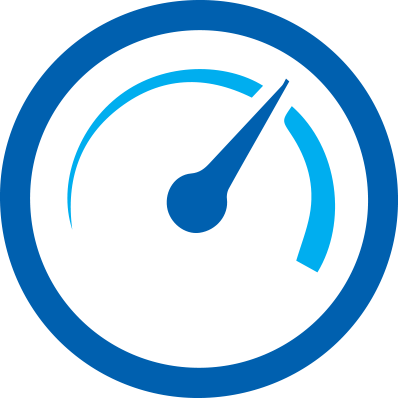
Total Dynamic Head is the amount of pressure differential created by a pump as it operates. Put simply, total dynamic head is a measurement of how much energy the pump will require to transport fluid to its final destination. The total Dynamic Head calculation is composed by the addition of vertical rise and friction loss.
Calculating Total Dynamic Head
Total dynamic head is calculated by adding together the vertical rise and friction loss. In an industrial pumping scenario vertical rise Is the height differential from the pumped liquid’s starting point to its destination. Since general pump applications often requires us to pump out of a container, vertical rise; and consequently, total dynamic head will increase as the liquid is pumped out of the container. Because of this when calculating TDH the worst-case scenario is assumed; we would measure as if the container is empty, unless there is certainty that the liquid level of the container will never diminish below a specific point.
As an example, let’s assume the following parameters: container 1 is 20 feet tall, and is filled to capacity at startup. The distance between the top of container 1 to the entry of container 2 in 10 feet. The pump is positioned 1-foot underneath container 1 and 31 feet underneath container 2. In this scenario, the vertical rise is 10 feet when container 1 is filled at maximum capacity. When container 1 is half depleted of its contents, the vertical rise transitions from 10 feet to 20 feet (10-foot rise between the containers in addition to 10 feet from current liquid position to the top of the container), and again from 20 feet to 31 feet when the tank is empty. For selection purposes, the vertical rise of 31 feet would be applied since it is the maximum vertical rise the pump would encounter during operation.
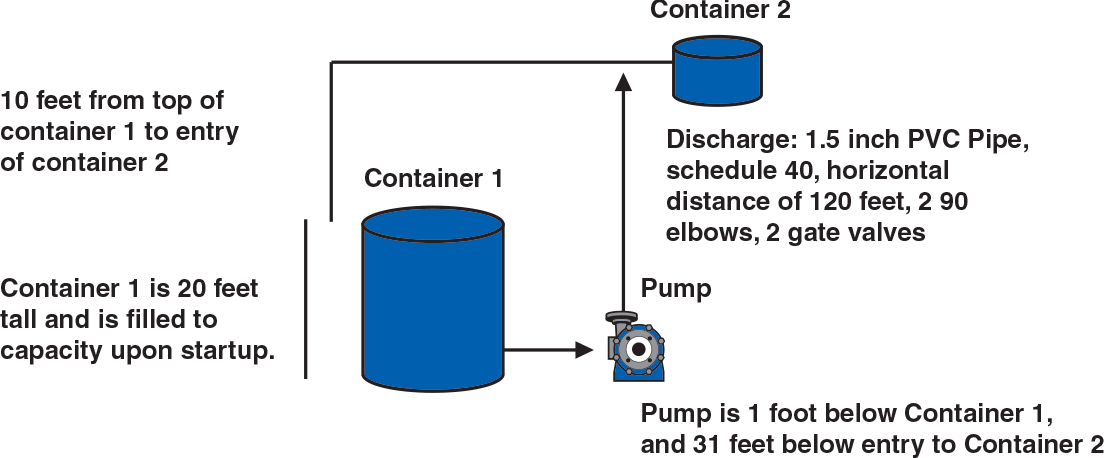
Friction loss, also referred to as head loss, is a measurement of resistance the pumped liquid encounters when traveling through the piping of an application. Calculating friction loss requires knowledge of the pipe size, schedule, material, and length; as well as knowledge of any valves or fittings. It is also important to know the flow rate, as greater flow rate through the same pipe will result in increased friction loss.
Using corresponding parameters from the previous example, assume we are pumping 25 gallons per minute through a discharge pipe that is 1.5-inch PVC, schedule 40, with a horizontal distance of 120 feet and a vertical distance of 31 feet, 2 90-degree elbows, and 2 gate valves..
We begin by calculating the total distance of pipes, which is the sum of the 120-foot horizontal distance in addition to the 31-foot vertical distance resulting in 152 feet of piping for this application.
We then enter this information in this head loss calculator, and click calculate.
The result is a head loss of 6 feet.
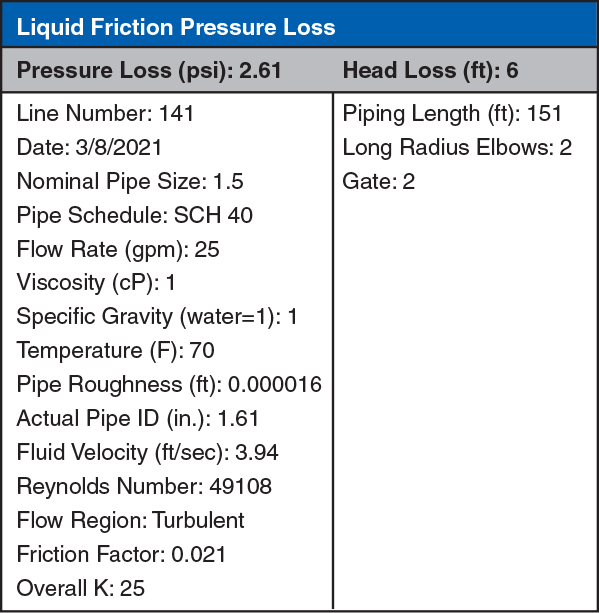
Total dynamic head is then the sum of the worst-case vertical rise (31 feet) and the head loss of (6 feet) resulting in 37 feet of total dynamic head. When calculating total dynamic head, it is important to take into consideration particular attributes of the pumped fluid due to its effect on friction loss within the piping system.
Other Total Dynamic Head Calculation Considerations
Pumped fluid’s temperature, viscosity, and specific gravity will affect friction loss and consequently TDH.
A liquid’s specific gravity only slightly influences friction loss; therefore, for fluids with specific gravity between 1.0 (water) and 2.0 accounting for viscosity in the calculation is unnecessary, but if the specific gravity is fewer than 1.0 or greater than 2.0 we encourage using an online calculator. Conversely, viscosity can greatly escalate friction losses. For viscous liquids, it is important to use a viscous specific gravity chart and incorporate viscosity into the friction loss calculator. The changes to friction loss based on the pumped fluid’s attributes plays a considerable role in selection of style of pump to use. For fluids with low viscosity (for example water or acids) we generally use a centrifugal pump such as our Edur or GemmeCotti pump lines, but for fluids with a high viscosity (for example lubrication oil) we generally use a positive displacement pump such as our Seim screw pump line. Shanley Pump has engineers on standby ready to answer any questions and offer the right pump for your application. Use the form below or call us at 847-439-9200.